Single cylinder cone crusher
Applicable materials: pebbles, bluestone, limestone, river pebbles, quartz sand, marble, wollastonite, calcite
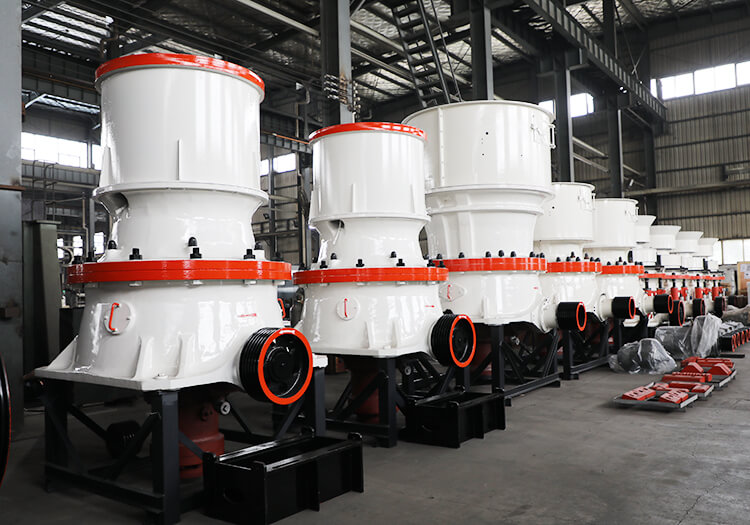
Applicable materials: pebbles, bluestone, limestone, river pebbles, quartz sand, marble, wollastonite, calcite
Single-cylinder cone crusher, also known as single-cylinder hydraulic cone crusher, is a highly efficient rock crusher commonly used in ore crushing, aggregate production, and construction waste recycling. It is mainly used for medium and fine crushing, and can sometimes be applied to the fourth stage of crushing. This crusher is particularly effective for crushing medium-hard rocks, stones, and minerals.
Single-cylinder cone crusher is widely used to crush metal and non-metallic ores such as iron ore, copper ore, and quartz. It is also suitable for aggregates such as granite and basalt, as well as construction waste such as concrete and asphalt.
However, it is not suitable for soft, wet or sticky materials such as clay or shale, because these materials will clog the machine and reduce efficiency.
Scope of application: construction, hydropower, transportation, chemistry, building materials and other industries
Finished product specifications: 0-10mm, 10-20mm, 20-30mm, 30-40mm
High Efficiency: Combining advanced chamber design and high crushing frequency, it can reach up to 2181 tons per hour.
Better Product Shape: Use intergranular lamination crushing to produce cubic final products with fewer needle-like particles.
Easy Maintenance: Components are easily removed from the top. No filler liner saves replacement time and cost.
Low Downtime: Equipped with hydraulic and lubrication systems, it provides double protection, automatically handles overloads and ensures continuous operation, reducing downtime.
Dustproof: Positive pressure system blocks dust and debris, keeps components clean and extends service life.
Intelligent Automation: With an intuitive interface, it can quickly adjust the discharge volume and precisely control the size. Automation increases productivity by 15%-25% and simplifies complex operations.
The cone crusher consists of key components such as the main shaft, casing, drum liner, concave surface, eccentric bushing and drive mechanism.
The single cylinder cone crusher consists of a series of key components working together to achieve efficient crushing. Understanding these components and their functions is essential for equipment selection:
Spindle
Made of high-strength steel, it provides core support and load-bearing capacity. It supports the moving cone for swinging motion and drives the material to be crushed through the eccentric mechanism.
Main frame
As the main structural foundation of the crusher, it accommodates core components such as concave liner and eccentric bushing, and bears various loads during the crushing process to ensure overall stability.
Moving cone
Together with the concave liner, it forms the crushing chamber. Made of highly wear-resistant materials (such as high manganese steel), it directly crushes materials through compression, and its wear resistance directly affects the life of the equipment.
Concave lining
It is usually cast as an integrated structure, providing a stable support surface for the crushing chamber and cooperating with the moving cone to crush materials. Its design directly affects the product particle size and production capacity.
Eccentric bushing
The core transmission component converts the rotation of the motor into the eccentric swing required by the moving cone. It usually adopts a high-carbon steel shell with a bronze lining. The eccentricity can be adjusted by replacing bushings of different sizes, thereby changing the crushing cavity shape and discharge port size to meet different particle sizes and production capacity requirements (such as from ultra-fine to medium crushing).
Driving mechanism
Efficiently transmit motor power to the eccentric bushing, ensuring smooth operation of the crusher and reducing energy consumption.
When selecting, you need to comprehensively evaluate the following key factors to ensure that the equipment fits your production goals, material characteristics and operating budget:
Determine the required capacity (t/h). Single-cylinder cone crushers cover a wide range of models. For example, in hard rock crushing applications such as granite, they can stably achieve a processing capacity of 25 to 2181 t/h to meet the needs of different scales.
Single-cylinder cone crushers are particularly good at processing granite, basalt and other medium-to-high hardness and highly abrasive materials. Their high-manganese steel cone and concave liner provide excellent wear resistance. They also perform well in the recycling of medium-hard materials such as construction waste and can provide stable output (such as about 200 t/h). Please note that sticky or high-moisture materials may not be suitable.
According to the maximum feed size and target product size, select the matching crushing chamber type (standard medium crushing, medium fine crushing, fine crushing or ultra-fine crushing). In the production line where the finished product particle size needs to be precisely controlled (such as 5-20mm or 10-30mm), choosing the right chamber type is very important.
Single-cylinder cone crushers have a relatively simple structure and their initial cost is usually lower than that of multi-cylinder models, making them the preferred choice for projects with strict budget control.
Its design significantly reduces maintenance difficulty and cost:
The packing-free design makes liner replacement faster and significantly reduces downtime.
Equipped with a remote touch screen control system, the eccentricity can be adjusted directly during operation (changing the discharge opening) without stopping the machine to replace parts, which significantly improves equipment utilization (extends normal operating time).
For mobile production line needs (such as multi-site construction waste processing), mobile single-cylinder cone crusher units provide great flexibility and deployment efficiency.
Be sure to choose a manufacturer with strong technical strength, reliable production scale and perfect after-sales service. Zoomjo has a good market reputation and global service capabilities, and can provide more lasting technical support and spare parts guarantee.
project | materials | Key Parameters | Solution |
---|---|---|---|
A large fixed granite crushing production line | High hardness granite | Processing capacity ~500 t/h; Feed size ≤250mm; Product size 5-20mm | Use single cylinder cone crusher for medium and fine crushing |
Operation effect: The equipment exhibits excellent wear resistance, can efficiently process high-hardness granite, operates continuously and stably with low maintenance requirements, significantly reducing the customer's overall operating costs and meeting the production requirements of high-quality aggregates.
project | materials | Key Parameters | Solution |
---|---|---|---|
Recycling and treatment of construction waste at multiple construction sites | Medium hardness construction waste (concrete blocks, bricks, etc.) | Processing capacity ~200 t/h; Feed size ≤180mm; Product size 10-30mm (can be used as recycled aggregate) | Use mobile single cylinder cone crusher unit |
Operation effect: The mobility of the equipment greatly improves the flexibility of deployment at different project sites. When crushing medium-hard construction waste, the output is stable and meets the standards, and the product particle size meets the requirements for recycling, meeting the core needs of customers for efficient operation at dispersed sites.
Model | Cavity Type | Maximum Feed Size(mm) | Minimum Discharge Size(mm) | Capacity (t/h) | Maximum Installed Power(kw) |
---|---|---|---|---|---|
CS420 | S1 (Extra coarse) S2 (Medium coarse) | 240 200 | 22 19 | 85-170 70-130 | 90 |
CH420 | H1 (Fine) H2 (Medium fine) H3 (Extra fine) | 135 65 38 | 10 8 4 | 45-130 35-80 27-60 | 90 |
CH430 | S1 (Extra coarse) S2 (Medium coarse) S3 (Coarse) | 360 300 235 | 25 22 19 | 120-345 105-305 90-275 | 160 |
CS430 | H1 (Fine) H2 (Medium fine) H3 (Extra fine) | 185 90 50 | 13 10 6 | 60-210 65-165 48-105 | 160 |
CH440 | S1 (Extra coarse) S2 (Medium coarse) S3 (Coarse) | 450 400 300 | 35 29 25 | 255-605 215-515 190-490 | 250 |
CS440 | H1 (Fine) H2 (Medium fine) H3 (Extra fine) | 215 110 70 | 16 13 8 | 110-395 115-340 90-225 | 250 |
CH660 | S1 (Extra coarse) S2 (Medium coarse) | 560 500 | 41 38 | 355-1050 305-895 | 315 |
CS660 | H1 (Fine) H2 (Medium fine) H3 (Extra coarse) | 275 135 65 | 16 16 13 | 170-665 190-505 205-320 | 315 |
Structure and hydraulic system: Single-cylinder machines have only one main hydraulic cylinder for adjusting the discharge port and iron protection, with a simpler structure and easier maintenance. Multi-cylinder machines have multiple hydraulic cylinders arranged around the main axis, providing greater locking force and more precise control.
Performance focus: Single-cylinder machines have high efficiency and low energy consumption in the field of medium and fine crushing, and are particularly suitable for materials that require good particle shape and medium or above hardness (such as the aforementioned granite and construction waste). Multi-cylinder machines perform better in high-capacity, ultra-high hardness materials or heavy-duty crushing tasks that require extreme stability.
Cost: Single-cylinder machines are generally more economical in terms of initial purchase and maintenance costs, making them an advantageous alternative to multi-cylinder machines.
The maintenance of a single cylinder cone crusher is relatively straightforward and is the key to its low operating costs:
Regular lubrication: Check and replace lubricating oil strictly according to regulations to ensure long-life and smooth operation of key components such as bearings and gears.
Wear parts inspection: Check the wear of the moving cone, concave liner and other wearing parts regularly (such as every shift or every day), and replace them in time to avoid reduced crushing efficiency and equipment damage. Thanks to its design, the liner replacement process has been optimized.
Crushing chamber cleaning: clean the residual materials in the chamber when the machine is shut down to prevent blockage, arching and abnormal wear.
System monitoring: Use the control system to monitor the operating status (such as discharge port setting, hydraulic pressure, temperature, vibration, etc.) to ensure that functions such as overload protection are normal.
Thanks to its simple structure and intelligent control features, the daily maintenance workload of the single-cylinder cone crusher is relatively small, and the maintenance cost is competitive among similar equipment. Its stable and reliable operation record (such as long-term trouble-free operation) also confirms its low maintenance requirements.
Directly contact us with your needs and get a solution in seconds!
E-mail: sales-zjks@zoomjo.cn
Tel: +86-371-87087999
Mobile: +86-15670952888
WhatsApp: +86-13938216895
TikTok
Copyright © Henan ZOOMJO MINING Machinery Co., Ltd. All Rights Reserved.