Rotary kiln
Applicable materials:calcined of cement clinker, roasting in metallurgical industry, roasting in refractory materials, roasting in chemical plants
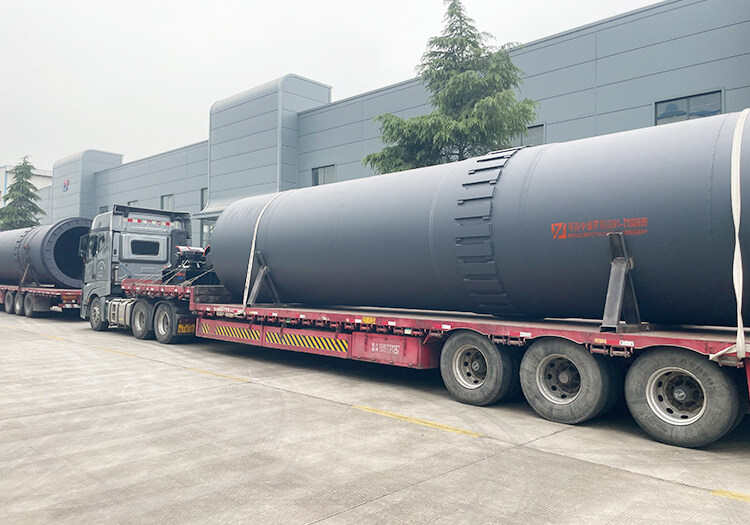
Applicable materials:calcined of cement clinker, roasting in metallurgical industry, roasting in refractory materials, roasting in chemical plants
Rotary kilns are processing equipment that heat materials to high temperatures through continuous calcination. They can also be used in the early stage of metal extraction by roasting sulfide ores in various ways to prepare ores for smelting.
Rotary kilns are used only as a vessel to cause chemical reactions or phase changes. Some processes using the rotary kiln are described as follows.
It is a process of chemical dissociation of materials (such as limestone, dolomite and magnesite) by heating them to a specific temperature. It also removes bound moisture, such as that chemically attached to borax.
Rotary kilns are used as reduction furnaces to remove oxygen (O2) from ore components using a reducing agent such as carbon monoxide (CO). Common processes include the reduction of iron ore pellets, barite and zinc-lead residues..
Thermal desorption uses heat to remove volatile components without the material coming into contact with the flame. It is the best way to handle non-metallic minerals such as kaolin, agricultural waste, mineral coatings, and wastewater sediments.
The most commonly used rotary kiln is an indirect rotary kiln designed based on physical and chemical properties and the calcination curve of the raw materials.
When the volume of waste is large and difficult to handle, organic combustion turns the materials into light ash. Therefore, the organic combustion method can more effectively deposit waste in landfills.
Sintering is a process of heating the material to a certain temperature before melting to increase its strength. Its most common application is to manufacture artificial proppant (a solid material, usually sand or artificial ceramic materials, intended to keep the induced hydraulic fractures open during or after the fracturing treatment).
In addition, rotary kilns have other applications, such as ilmenite, calcined petroleum coke, and volatile zinc oxide.
Depending on the type of materials, they can be classified into three types: lime kilns, cement kilns and metallurgical and chemical kilns. Kiln capacities range from 180 to 10,000 tons per hour.
Lime kiln (also known as active lime kiln) is the core equipment for calcining active lime and light-burned dolomite in steel plants, ferroalloy plants, calcium carbide plants, and magnesium plants.
Cement kiln is a cement machine used to produce cement clinker, which can be divided into dry cement kiln and wet cement kiln. Clinker includes limestone, clay, gypsum, shale, etc. Limestone is an important raw material for cement, and calcined clay is often used as a clinker substitute in many countries.
Metallurgical and chemical kilns can roast minerals such as kaolin, magnesite, bauxite, lithium ore, lean iron ore, chromium ore, nickel iron ore, etc., which are used in steel mills, refractory plants and chemical plants. It also determines the performance of lightweight expanded clay aggregate (LECA).
1. Ceramic lining
It adopts 70% alumina refractory bricks to prevent high-temperature corrosion and extend the service life of the kiln body.
2. Kiln shell
Automatically welded with high-quality low-carbon steel plates. Equipped with solid tires to enhance rigidity and reduce thermal deformation stress.
3. Large gear ring
Connected to the kiln shell through spring plates, it serves for heat dissipation and buffering, ensuring transmission accuracy and protecting the kiln lining.
4. Drive device
It consists of the main drive (motor + reducer + pinion + coupling) and the auxiliary drive.
5. Supporting device
Load-bearing main body, including support wheel bearings and welded base, ensuring stable operation.
6. Hydraulic Grab Wheel
Standard equipment for large kilns, consisting of grab wheel, shaft, bearing body, etc., available in mechanical and hydraulic forms.
7. Sealing system
Kiln head / kiln tail sealing device to prevent air leakage and dust spillage.
Intelligent control: Precisely adjust temperature, speed and axial movement, meeting diverse production demands.
High-efficiency production capacity: Processing capacity reaches 180 - 10,000 tons/hour, covering a wide range of industrial scenarios.
Weather resistant design: Suitable for corrosive materials and extreme process environments with high reliability.
Energy-saving heating: calcination/sintering/pyrolysis multi-mode, even heat distribution, low energy consumption.
Long-lasting and durable: highly wear-resistant, bending-resistant, high-temperature-resistant, low failure rate, easy maintenance.
Environmentally friendly production: optimized sealing system + new type of dust removal to achieve zero pollution emission.
Product Specification | Motor Power (kw) | Total Weight (t) | Note | Kiln Dimensions | ||||
---|---|---|---|---|---|---|---|---|
Diameter (m) | Length (m) | Obliquity (%) | Capacity (t/d) | Rotation Speed (r/min) | ||||
φ2.5×40 | 2.5 | 40 | 3.5 | 180 | 0.44-4.5 | 55 | 149.61 | |
φ2.5×50 | 2.5 | 50 | 3 | 200 | 0.62-4.5 | 55 | 187.37 | |
φ2.5×54 | 2.5 | 54 | 3.5 | 280 | 0.48-4.5 | 55 | 196.29 | Outside Disassemble Kiln |
φ2.7×42 | 2.7 | 42 | 3.5 | 320 | 0.10-4.5 | 55 | 198.5 | |
φ2.8×44 | 2.8 | 44 | 3.5 | 450 | 0.437-4.5 | 55 | 201.58 | Outside Disassemble Kiln |
φ3.0×45 | 3 | 45 | 3.5 | 500 | 0.5-4.5 | 75 | 201.94 | |
φ3.0×48 | 3 | 48 | 3.5 | 700 | 0.6-4.5 | 100 | 237 | Outside Disassemble Kiln |
φ3.0×60 | 3 | 60 | 3.5 | 800 | 0.3-4.5 | 100 | 310 | |
φ3.2×50 | 3.2 | 50 | 4 | 1000 | 0.6-4.5 | 125 | 278 | Outside Disassemble Kiln |
φ3.3×52 | 3.3 | 52 | 3.5 | 1300 | 0.266-4.5 | 125 | 283 | Kiln with Preheater and Precalcine |
φ3.5×54 | 3.5 | 54 | 3.5 | 1500 | 0.55-4.5 | 220 | 363 | |
φ3.6×70 | 3.6 | 70 | 3.5 | 1800 | 0.25-4.5 | 125 | 419 | |
φ4.0×56 | 4 | 56 | 4 | 2300 | 0.41-4.5 | 315 | 456 | |
φ4.0×60 | 4 | 60 | 3.5 | 2500 | 0.396-4.5 | 315 | 510 | |
φ4.2×60 | 4.2 | 60 | 4 | 2750 | 0.41-4.5 | 375 | 633 | |
φ4.3×60 | 4.3 | 60 | 3.5 | 3200 | 0.396-4.5 | 375 | 583 | |
φ4.5×66 | 4.5 | 66 | 3.5 | 4000 | 0.41-4.5 | 560 | 710.4 | |
φ4.7×74 | 4.7 | 74 | 4 | 4500 | 0.35-4.5 | 630 | 849 | |
φ4.8×74 | 4.8 | 74 | 4 | 5000 | 0.396-4.5 | 630 | 899 | |
φ5.0×74 | 5 | 74 | 4 | 6000 | 0.35-4.5 | 710 | 944 | |
φ5.6×87 | 5.6 | 87 | 4 | 8000 | Max4.5 | 800 | 1265 | |
φ6.0×95 | 6 | 95 | 4 | 10000 | Max5 | 950×2 | 1659 |
Directly contact us with your needs and get a solution in seconds!
E-mail: sales-zjks@zoomjo.cn
Tel: +86-371-87087999
Mobile: +86-15670952888
WhatsApp: +86-13938216895
TikTok
Copyright © Henan ZOOMJO MINING Machinery Co., Ltd. All Rights Reserved.