Ball mill
Applicable materials: various ores, gold, silver, copper, iron, various metal beneficiation, cement, fertilizer, silicate products, refractory materials, glass, etc.
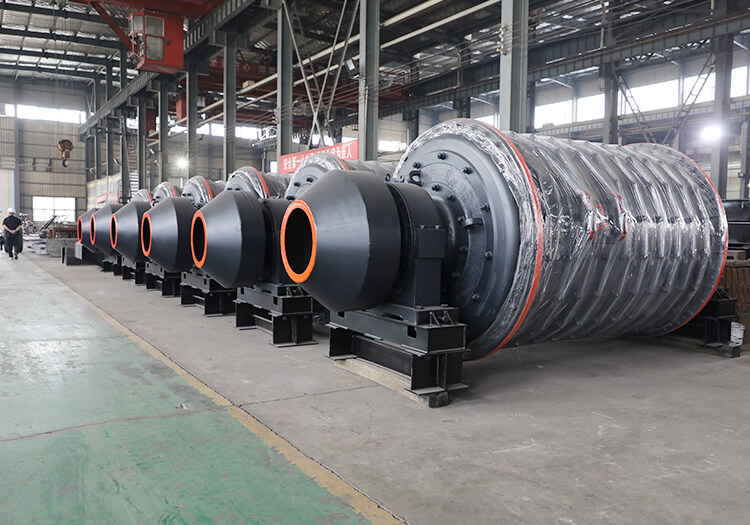
Applicable materials: various ores, gold, silver, copper, iron, various metal beneficiation, cement, fertilizer, silicate products, refractory materials, glass, etc.
The ball mill is a grinding machine that reduces the size of materials by using a rotating cylinder filled with grinding media such as steel or ceramic balls.
Ball mills are mainly used for crushing and grinding materials. They can process feed from a jaw crusher in the coarse crushing stage or feed from other grinding equipment such as a rod mill or SAG mill in the fine crushing stage.
Mining Processing
Widely used for grinding metal ores such as gold, copper, and iron, and non-metallic minerals such as bentonite and kaolin, and working with crushing, flotation, magnetic separation and other equipment to improve the efficiency of mineral extraction.
Cement production
Grinding clinker, gypsum and additives such as slag/fly ash to optimize cement strength and durability.
Fertilizer manufacturing
Crush phosphate rock/limestone raw materials and evenly mix urea/ammonium nitrate to ensure fertilizer quality.
Ceramic Industry
Finely grind raw materials such as feldspar and quartz to form a uniform slurry to improve the consistency and durability of the finished product.
Extended Applications
It has both mixing and dispersing functions, and is suitable for coal coke grinding, building materials processing, and auxiliary production in the fields of chemical, pharmaceutical, and food.
There are many types of ball mills according to application and process requirements. The following are types classified by process conditions, structural form, grinding media and aspect ratio of the drum.
Dry ball mill: Grinds material into mineral powder of desired fineness. Dry ball mills are suitable for hard materials such as silica sand, quartz, marble and cement clinker.
Wet ball mill: Grinds material into slurry of specific concentration (usually 60%–70%). Wet ball mills are commonly used for mineral processing and usually have a single chamber structure.
Overflow ball mill: produces finer grinding results and is suitable for the second stage of a two-stage grinding process. The feed particle size is usually less than 0.2 mm. Its output is about 15% lower than that of a mesh ball mill of the same size, and it also uses less grinding media.
Mesh ball mill: suitable for situations where the product particle size is 0.2 mm–0.3 mm and needs to be uniform. This type of mill can quickly discharge qualified products, reduce over-grinding, and improve grinding efficiency. It is usually used for the first stage of grinding.
Ball mill: uses cast grinding steel balls and forged grinding steel balls as grinding media.
Rod mill: uses grinding rods and grinding cylpebs as grinding media.
Ceramic ball mill: uses ceramic balls as grinding media.
Ball mill: A typical ball mill has a drum length equal to or equal to 1.5 times the drum diameter.
Tube mill: A mill with a drum length-to-diameter ratio greater than 1.5 is called a tube mill.
A ball mill consists of several important parts: the cylinder, grinding media, drive system, feed and discharge ports, bearings and liners.
The cylinder is the main working part of the ball mill, where the grinding process takes place. It is a cylindrical structure, usually made of steel plates. The inside of the cylinder is lined with gaskets to protect its inner wall.
Grinding media, usually steel or ceramic balls, are used to grind the material. The type and size of these balls will affect the grinding efficiency. Selecting the appropriate ball type, size, and ratio of large, medium, and small balls should be based on the material being ground.
Liners are installed inside the cylinder to protect it from wear and to help the grinding media move. They can be made of alumina ceramic, high manganese steel, rubber, quartz, SILEX or special materials. For grinding hard minerals, iron-free designs are often used.
The drive system provides power to the ball mill, including the motor, gearbox, gears and basic control system. The motor drives the large gear through the reducer, which rotates the cylinder and drives the grinding media and materials in the mill.
The feed port is located at one end of the cylinder and is equipped with a feed screw to increase the feed rate. The discharge port at the other end releases the ground material and is usually equipped with a screen or overflow device to control the particle size.
Bearings support the rotating cylinder. Using rolling bearings instead of traditional sliding bearings reduces energy consumption by 15%-20%. Small ball mills use anti-friction cylindrical roller bearings, while large ball mills use trunnion and hydrostatic bearings.
ZOOMJO GROUP is committed to providing efficient and reliable solutions. With more than 40 years of experience in ball mill technology, we produce durable and sturdy ball mills that provide higher value at lower costs.
High production capacity: Capable of continuous operation, with a maximum processing capacity of up to 615 t/h, meeting large-scale production needs.
Energy efficiency:Rolling bearings replace traditional sliding bearings, reducing energy consumption by 15%–20%.
Durable components:Liners and discharge grids use advanced casting and heat treatment technology to minimize wear during operation.
Flexible design: Choose between grid or overflow discharge, and screw forced feed for increased feed capacity. Optional iron separator available.
Dry oil lubrication system:large and small gears are lubricated by dry oil spray, which is highly efficient, low in oil consumption, compact in design and leak-free.
Environmental protection: The ball mill and classifier form a closed system with negative pressure conveying, which reduces dust and makes it suitable for handling toxic substances.
Quality service:ZOOMJO GROUP provides sufficient supply of parts, including large and small gears, steel balls and bearings, to minimize maintenance and replacement time.
Model | Cylinder size(m) | Speed (r/min) | Ball loading(t) | Feed size(mm) | Discharge Size(mm) | Capacity (t/h) | Power (kw) |
---|---|---|---|---|---|---|---|
MQZ1224 | 1.2X2.4 | 31 | 4.8 | 0-20 | 0.07-0.6 | 0.4-6.8 | 37 |
MQZ1245 | 1.2X4.5 | 31 | 5.2 | 0-20 | 0.07-0.6 | 1.6-12 | 45 |
MQZ1530 | 1.5X3.0 | 27.5 | 8.1 | 0-25 | 0.07-0.4 | 2.9-16.5 | 65 |
MQZ1557 | 1.5X5.7 | 29.2 | 15 | 0-25 | 0.07-0.4 | 4-25 | 95 |
MQZ1645 | 1.6X4.5 | 27.5 | 14 | 0-25 | 0.07-0.4 | 4-24 | 95 |
MQZ1836 | 1.8X3.6 | 23.9 | 11 | 0-25 | 0.07-0.4 | 8-40 | 132 |
MQZ1864 | 1.6X6.4 | 23.9 | 18.5 | 0-25 | 0.07-0.4 | 8-60 | 155 |
MQZ2130 | 2.1X3.0 | 23.8 | 19.8 | 0-25 | 0.07-0.4 | 6.5-36 | 155 |
MQZ2136 | 2.1X3.6 | 23.8 | 27 | 0-25 | 0.07-0.4 | 8-61 | 155 |
MQZ2265 | 2.2X6.5 | 21.6 | 28 | 0-25 | 0.07-0.4 | 8-35 | 210 |
MQZ2430 | 2.4X3.0 | 22 | 22.5 | 0-25 | 0.07-0.4 | 7-92 | 210 |
MQZ2436 | 2.4X3.6 | 22 | 28 | 0-25 | 0.07-0.4 | 7-95 | 210 |
MQZ2465 | 2.4X6.5 | 22 | 36 | 0-25 | 0.07-0.4 | 7-110 | 260 |
MQZ2736 | 2.7X3.6 | 21.9 | 39 | 0-25 | 0.07-0.4 | 13-140 | 310 |
MQZ2745 | 2.7X4.5 | 21.9 | 43 | 0-25 | 0.07-0.4 | 13-150 | 320 |
MQZ2836 | 2.8X3.6 | 20 | 42 | 0-25 | 0.07-0.4 | 15-140 | 310 |
MQZ3060 | 3.0X6.0 | 19 | 70 | 0-25 | 0.07-0.4 | 100-145 | 630 |
MQZ3245 | 3.2X4.5 | 18.6 | 65 | 0-25 | 0.07-0.4 | 100-145 | 630 |
MQZ3260 | 3.2X6.0 | 18.6 | 86 | 0-25 | 0.07-0.4 | 120-150 | 800 |
MQZ3645 | 3.6X4.5 | 17.8 | 90 | 0-25 | 0.07-0.4 | 120-220 | 1000 |
MQZ3660 | 3.6X6.0 | 17.8 | 120 | 0-25 | 0.07-0.4 | 50-230 | 1250 |
Directly contact us with your needs and get a solution in seconds!
E-mail: sales-zjks@zoomjo.cn
Tel: +86-371-87087999
Mobile: +86-15670952888
WhatsApp: +86-13938216895
TikTok
Copyright © Henan ZOOMJO MINING Machinery Co., Ltd. All Rights Reserved.