Zambia Copperbelt Province High-efficiency Grinding Project
Zambia's Copperbelt Province has the largest barite reserves in Africa, but the local processing technology is backward, and the products are limited to coarse powder (80-200 mesh), with extremely low added value. In 2022, ZOOMJO GROUP will build an intelligent barite deep processing base for Mining Pro to address the problems of frequent power fluctuations in the mining area and high silicon impurities in raw materials (8-12%). It will be equipped with 2 fully automatic production lines to achieve integrated production of crushing-purification-ultrafine grinding-modification treatment, helping customers transform from traditional mining to high value-added fields.
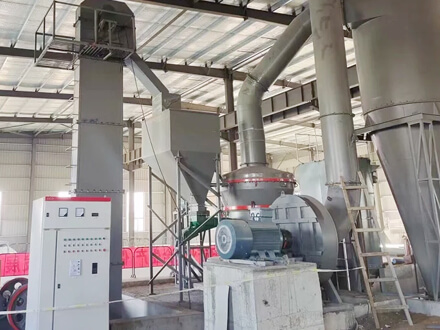
Customer feedback
"The barite Raymond mill production line designed by ZOOMJO GROUP has completely overturned our expectations! The production line has a high degree of automation, the unit energy consumption is reduced by 30%, and the error of the finished product particle size uniformity is less than ±2%. The intelligent temperature control system ensures that the mill can operate stably in a high temperature environment of 45°C, and the dust emission is only 2mg/m³, far exceeding the ISO environmental protection standard. Since it was put into production in 2023, the 600-mesh ultrafine powder has successfully entered the European high-end coatings market, and the annual export volume has increased by 200%!" - Daniel Banda, General Manager of Mining Pro Company in Zambia
Project Overview
Zambia's Copperbelt Province has the largest barite reserves in Africa, but the local processing technology is backward, and the products are limited to coarse powder (80-200 mesh), with extremely low added value. In 2022, ZOOMJO GROUP will build an intelligent barite deep processing base for Mining Pro to address the problems of frequent power fluctuations in the mining area and high silicon impurities in raw materials (8-12%). It will be equipped with 2 fully automatic production lines to achieve integrated production of crushing-purification-ultrafine grinding-modification treatment, helping customers transform from traditional mining to high value-added fields.
Production line process
1. Efficient crushing and purification
Jaw crusher: The raw ore is crushed to ≤30mm by jaw crusher. The crushing chamber adopts high manganese steel + ceramic composite lining, and the wear resistance life is increased by 5 times.
Stepped impurity removal: After crushing, the material passes through a dual-channel high-gradient magnetic separator (iron content <0.3%) and an air flow separator (to remove quartz sand impurities), and the purity is increased to 99.2%.
2. Raymond mill ultrafine grinding
Intelligent classification: integrated turbine ultrafine classifier, dynamic adjustment of blade inclination angle through hydraulic servo system, finished product fineness covers 400-600 mesh, specific surface area reaches 4500cm²/g.
Anti-interference design: equipped with wide voltage motor (300-500V adaptive) and energy storage buffer device to adapt to African power grid fluctuations.
Online modification: through the automatic surfactant addition system, the compatibility of powder and resin is improved, and the activation index is ≥97%.
3. Precision grading and packaging
Multi-stage dynamic powder selection: laser particle size analyzer + AI feedback control is used, 600 mesh powder accounts for ≥98%, and fineness error is <±1.5%.
Zero leakage collection: finished products are collected by negative pressure pulse dust removal system (filtration accuracy 0.3μm), and exhaust emissions are <3mg/m³.
Moisture-proof packaging: vacuum ton bag packaging line is used, and the moisture content is controlled to <0.5%, which supports the moisture-proof needs of sea transportation.
Technical highlights
African adaptability: The device shell adopts nano-rust-proof coating, and the key circuit boards are equipped with dust-proof and insect-proof modules to adapt to the tropical savanna climate.
Circular production: sorting tailings for hardening of mining roads, waste heat recovery for pre-drying of raw materials, and the comprehensive utilization rate of solid waste reaches 95%.