Vietnam Da Nang High-Efficiency Cement Project
The dry process cement production line of ZOOMJO GROUP has revolutionized our position in the industry! The intelligent design of the whole process from limestone crushing to clinker calcination reduces heat consumption by 18%, and dust emission is only 8mg/m³, far exceeding the South TCVN environmental standards. The remote operation and maintenance system can monitor kiln temperature and mill vibration in real time, with 24-hour online support from Chinese engineers, and the operation rate of the production line has exceeded 98% in the past 3 years.
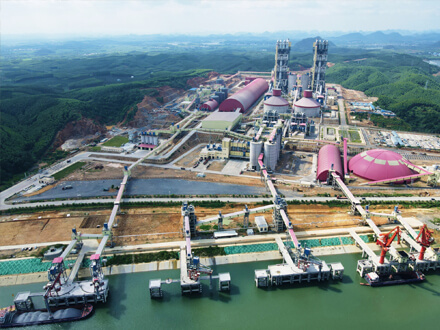
Customer Feedback
“ The dry process cement production line of ZOOMJO GROUP has revolutionized our position in the industry! The intelligent design of the whole process from limestone crushing to clinker calcination reduces heat consumption by 18%, and dust emission is only 8mg/m³, far exceeding the South TCVN environmental standards. The remote operation and maintenance system can monitor kiln temperature and mill vibration in real time, with 24-hour online support from Chinese engineers, and the operation rate of the production line has exceeded 98% in the past 3 years. ”
--Tran Duc Anh, Production Director, Vinacom Building Materials Group, Vietnam
Production Line Flow
1. Intelligent crushing and pre-homogenization
Graded crushing: Limestone is roughly crushed to ≤80mm by Jaw Crusher (JC120), and then finely crushed to ≤25mm by Multi-cylinder Hydraulic Cone Crusher.
Pre-homogenization yard: the crushed raw material enters the intelligent pre-homogenization warehouse, adopting the proportioning system, and the fluctuation of CaO is controlled <±0.3%.
2. Raw material preparation and preheating and decomposition
Vertical roller mill (LM56.3+3): grinding power consumption ≤28kWh/t, with gas box pulse dust collector, dust emission <10mg/m³.
Six-stage cyclone preheater: raw material is decomposed by CDC type decomposition furnace (decomposition rate ≥95%), and heat consumption is reduced to 2850kJ/kg-clinker.
3. Calcination and cooling of rotary kiln
Φ5.2×78m rotary kiln: adopting nano insulating lining, surface temperature reduced by 40℃, free calcium of clinker ≤1.0%.
Fourth generation grate cooler: heat recovery efficiency ≥75%, discharge temperature ≤65℃ + ambient temperature
4. Cement grinding and intelligent shipping
Roller press combined grinding system: the specific surface area of cement is controlled at 350±10m²/kg, and the power consumption per ton of powder is ≤32kWh.
Unattended transportation: Finished products are accurately measured by fully automatic loading system, and the transportation efficiency reaches 200t/h.
Technical Highlights
Low-carbon process: integrated biomass fuel substitution system (substitution rate ≥15%), clinker tons of CO₂ emissions down to 780kg.
Recycling ecology: kiln tail waste gas waste heat power generation (annual power supply 25GWh), dust recycling for road base materials, solid waste utilization rate of 100%.