South African kaolin Raymond mill case
Gauteng Province in South Africa has the largest kaolin deposit in Africa, but local processing plants generally face problems such as aging equipment, high energy consumption (electricity consumption per ton> 50kWh), and low product added value. In 2023, ZOOMJO GROUP will build an intelligent kaolin deep processing base for Highveld Company to address the challenges of high summer temperatures in the region (surface temperature reaches 45°C) and large fluctuations in the iron content of raw materials (0.5%-1.8%). It will be equipped with 3 fully automatic Raymond mill production lines to achieve integrated production of crushing-iron removal-ultrafine grinding-functional modification, and promote the upgrading of South African kaolin from traditional ceramic fillers to high-end cosmetics and pharmaceutical-grade raw materials.
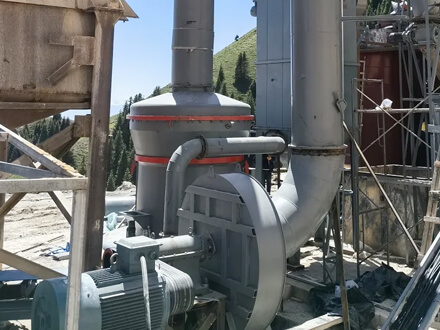
Customer feedback
"The Raymond mill production line of ZOOMJO GROUP completely solves the pain points of South African kaolin processing! The production line adopts a fully enclosed layout, with dust emissions as low as 3mg/m³, and easily passed the South African National Environmental Protection Agency (NEMA) certification. The intelligent central control system can monitor the operating parameters of the mill in real time, and remotely adjust the fineness and output through the mobile phone, with a failure rate of almost zero. Since it was put into production in 2024, the screening rate of 400-mesh ultrafine powder has reached 99.3%, and the whiteness has been stable at more than 90%, helping us become a core supplier of multinational companies such as Unilever and IKEA!" --Pieter van Wyk, technical director of Highveld Mining Company in South Africa
Project Overview
Gauteng Province in South Africa has the largest kaolin deposit in Africa, but local processing plants generally face problems such as aging equipment, high energy consumption (electricity consumption per ton> 50kWh), and low product added value. In 2023, ZOOMJO GROUP will build an intelligent kaolin deep processing base for Highveld Company to address the challenges of high summer temperatures in the region (surface temperature reaches 45°C) and large fluctuations in the iron content of raw materials (0.5%-1.8%). It will be equipped with 3 fully automatic Raymond mill production lines to achieve integrated production of crushing-iron removal-ultrafine grinding-functional modification, and promote the upgrading of South African kaolin from traditional ceramic fillers to high-end cosmetics and pharmaceutical-grade raw materials.
Production line process
1. Heavy crushing and purification
Jaw crusher: The raw ore is crushed to ≤200mm by jaw crusher, equipped with metal detector and hydraulic overload protection system, the crushing efficiency is increased by 40%
Stepwise iron removal: After crushing, the material passes through a three-channel high-gradient magnetic separator, and the iron content is stably controlled to <0.4%, meeting the standards for pharmaceutical-grade raw materials.
2. Raymond mill ultrafine grinding
Intelligent temperature control: The mill is equipped with a dual-circulation cooling system (air cooling + water cooling), which keeps the bearing temperature <75°C in a high temperature environment of 45°C.
Dynamic classification: Integrated turbine superfine classifier, the finished product fineness covers 80-400 mesh, and the unit power consumption is 35% lower than that of traditional Raymond mill.
Online modification: Stearic acid is added through surface coating technology to improve the hydrophobicity and dispersibility of powders above 325 mesh.
3. Precision grading and packaging
Multi-level dynamic powder selection: using laser particle size feedback + AI algorithm, 400 mesh powder accounts for ≥95%, particle size error <±1%.
Zero pollution collection: finished powder is collected by pulse bag dust collector, exhaust emission <3mg/m³, in line with EU ISO 8573-1 standard.
Smart packaging: using fully automatic ton bag packaging line, packaging accuracy ±0.3%.
Technical highlights
High temperature adaptability: The motor adopts H-class insulation coating, and the electric control cabinet has a built-in constant temperature and dustproof module to adapt to the extreme climate on the edge of the desert.
Smart operation and maintenance: Through the IoT predictive maintenance system, the accuracy of roller and blade wear warning is >90%, and the maintenance cost is reduced by 50%.
Circular economy: waste heat is used for raw material pre-drying through the waste heat recovery device, and the overall energy consumption is reduced by 25%; tailings are used for ecological brick manufacturing, and the comprehensive utilization rate of solid waste reaches 98%.