High Efficiency Ceramic Sand Project in Sumatra, Indonesia
The ceramic sand production line of ZOOMJO GROUP allows us to realize a technological leap in the Southeast Asian market! The whole line adopts intelligent design, the heat consumption is reduced by 25%, the compressive strength of the product reaches 52MPa, and the dust emission is only 3mg/m³, which far exceeds the environmental protection standard of SNI Indonesia.
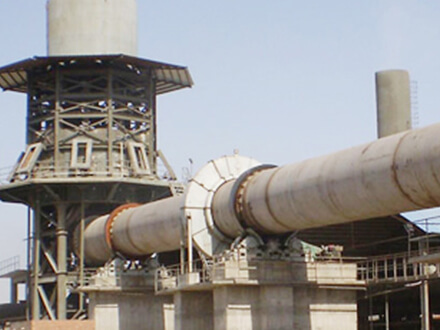
Customer Feedback
The ceramic sand production line of ZOOMJO GROUP allows us to realize a technological leap in the Southeast Asian market! The whole line adopts intelligent design, the heat consumption is reduced by 25%, the compressive strength of the product reaches 52MPa, and the dust emission is only 3mg/m³, which far exceeds the environmental protection standard of SNI Indonesia. --Agus Wijaya, Technical Director of Archipelago Building Materials Group, Indonesia
Production process
1. Raw material pretreatment
Crushing process
Bauxite raw materials (block size 300-500mm) are crushed by jaw crusher. After crushing, the materials are temporarily stored in buffer bin, and some need to be dried (when moisture content > 6%).
Drying treatment
Broken bauxite is dried by waste heat from boiling furnace or rotary kiln, with hot air temperature of 800-900℃ to reduce the moisture content of the materials to the process requirements.
2. Batching and grinding
Batching system
Bauxite is matched with manganese powder, recycled materials, etc. in proportion, and automatic metering is achieved through speed-adjustable belt scale. Manganese element is used to reduce sintering temperature and enhance product coloring.
Grinding process
A closed-circuit grinding system consisting of ball mill and high-efficiency powder selector is used. The raw material powder fineness reaches more than 400 mesh, and the heat source can come from rotary kiln exhaust gas or special hot air furnace.
3. Ball making and calcining
Ball making process
The raw material powder is added with water through a disc ball making machine to make balls with uniform particle size. After screening, qualified balls (particle size meets the standard) enter the rotary kiln, and oversized particles return to the grinding system.
Rotary kiln calcination
The balls are calcined at high temperature (1200-1500℃) in an inclined rotary kiln. The fuel can be coal powder, gas or fuel oil to form high-strength ceramsite sand.
4. Cooling and post-processing
Cooling system
The high-temperature ceramsite sand is cooled to room temperature by a single cooler or naturally to prevent thermal stress from causing particle breakage.
Screening and packaging
After cooling, the material is graded by particle size (such as 20/40 mesh, 30/50 mesh, etc.) through a cylindrical screen. Qualified products are packaged and stored, and unqualified particles are returned to the grinding or ball making process.