Copper and Cobalt Ore Beneficiation Production Line Site in Central African Congo (DRC)
Congo (DRC) has rich reserves of copper and cobalt ore resources, but local ore dressing plants generally face the challenges of complex ore composition and low recovery rate. In order to enhance the competitiveness of customers,ZOOMJO GROUP designed an efficient and energy-saving joint production line for them. By optimizing equipment selection and process flow, it significantly improved the copper-cobalt separation efficiency and concentrate grade, helping customers gain a technical advantage in the regional market.
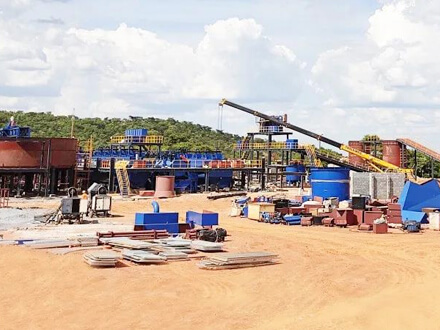
Project details
Congo (DRC) has rich reserves of copper and cobalt ore resources, but local ore dressing plants generally face the challenges of complex ore composition and low recovery rate. In order to enhance the competitiveness of customers,ZOOMJO GROUP designed an efficient and energy-saving joint production line for them. By optimizing equipment selection and process flow, it significantly improved the copper-cobalt separation efficiency and concentrate grade, helping customers gain a technical advantage in the regional market.
Production line process
Crushing stage: The raw ore is coarsely crushed by a jaw crusher, then medium and finely crushed by a cone crusher, and finally the ore that meets the particle size requirements is screened out by a vibrating screen.
Grinding and classification: Qualified ore enters the ball mill for wet grinding and is matched with a hydrocyclone to form a closed-loop circulation to ensure that the slurry fineness meets the flotation requirements.
Flotation separation: After the slurry is mixed with customized reagents in a mixing barrel, it enters the flotation machine to prioritize copper and obtain copper concentrate; the tailings are then adjusted for pH value and cobalt minerals are floated to achieve efficient separation of copper and cobalt.
Concentration and dehydration: The copper and cobalt concentrates after flotation are precipitated by high-efficiency concentrators, dehydrated by filter presses, and finally dried into concentrate powder with a moisture content of less than 8%.
Results
Copper recovery rate increased to 92%, cobalt recovery rate reached 85%;
The concentrate grade increased by 15%-20% compared with the traditional process, and the customer's investment return cycle was shortened by 30%.
This project has become a benchmark case in the field of copper and cobalt beneficiation in the Democratic Republic of the Congo, providing a reliable solution for the subsequent processing of high-oxidation rate ores in Africa.