800 tons/day copper ore flotation production line in Atacama Desert, Chile
The Atacama Desert in Chile has the richest copper resources in the world, but the local extremely dry climate and environmental regulations place strict demands on mineral processing technology. The customer originally used a traditional fixed flotation plant, but due to water shortages and high tailings treatment costs, it decided to upgrade to a modular flotation production line provided by ZOOMJO GROUP. The solution integrates efficient crushing, water-saving grinding and intelligent flotation systems, reducing water consumption by 30% while ensuring production capacity, becoming a benchmark case for high environmental standards mining areas in South America10.
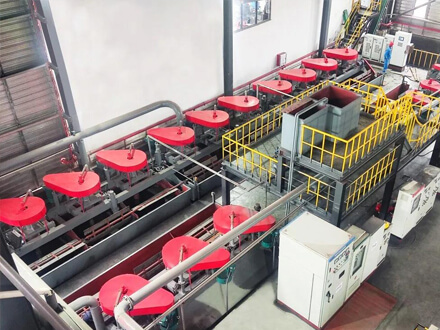
Customer feedback
"We chose the copper flotation production line of China's ZOOMJO GROUP not only because of its excellent production capacity (800 tons/day), but also because of its excellent environmental performance and low operating costs. Since the production line was put into operation in 2024, the copper recovery rate has remained stable at more than 92%, and the tailings treatment system has greatly reduced waste accumulation, fully meeting the strict standards of Chile's SEA (Environmental Assessment Agency). ZOOMJO GROUP's technical team also provided localized operation and maintenance training to ensure the long-term and efficient operation of the production line."
Project Background
The Atacama Desert in Chile has the richest copper resources in the world, but the local extremely dry climate and environmental regulations place strict demands on mineral processing technology. The customer originally used a traditional fixed flotation plant, but due to water shortages and high tailings treatment costs, it decided to upgrade to a modular flotation production line provided by ZOOMJO GROUP. The solution integrates efficient crushing, water-saving grinding and intelligent flotation systems, reducing water consumption by 30% while ensuring production capacity, becoming a benchmark case for high environmental standards mining areas in South America10.
Production line process
Coarse crushing stage
The raw ore (≤600mm) is initially crushed by a mobile jaw crusher (JC5460), and the discharge opening is hydraulically adjusted to 150mm, which is suitable for high-hardness porphyry copper ore.
Grinding and Classification
After crushing, the ore enters the energy-saving ball mill (MQY3660) for wet grinding, and is matched with a hydrocyclone for closed-circuit classification. The grinding fineness reaches -200 mesh, accounting for 70%, which saves 15% energy compared with the traditional process10.
Flotation separation
The ore pulp and customized collector (Z-200) are used to select copper in the XCF/KYF flotation machine. The “one roughing, two sweeping and three concentrating” process is adopted, and the concentrate grade is increased to 66.2%, and the copper content of the tailings is less than 0.15%.
Concentration and dehydration
The concentrate pulp is precipitated by a high-efficiency deep cone concentrator and then dehydrated by a plate and frame filter press. The final moisture content is ≤12% and is directly shipped for export.